Enhancing Energy Sector Resilience with Predictive Maintenance
This article delves into how predictive maintenance technologies are pivotal in transforming the energy sector by maximizing efficiency, reducing costs, and ensuring uninterrupted service.
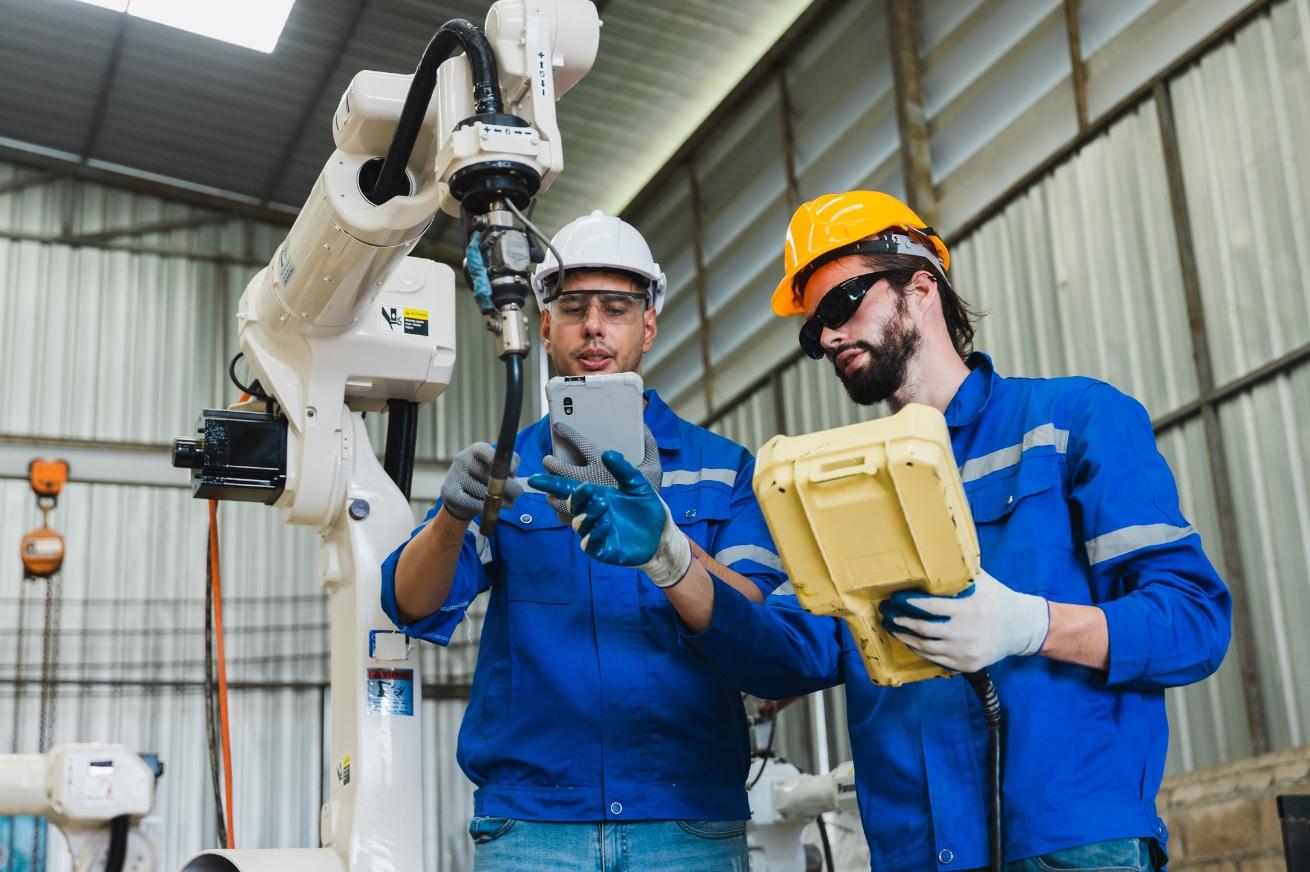
Predictive maintenance (PdM) is rapidly becoming a cornerstone technology in the energy sector, crucial for enhancing operational efficiencies and sustainability. Leveraging advanced artificial intelligence (AI) and machine learning (ML), predictive maintenance programs anticipate and mitigate potential failures before they disrupt operations.
Evolution of Maintenance Strategies
Historically, the energy sector relied on reactive maintenance models, addressing equipment failures as they occurred. This approach often led to unexpected outages and high repair costs. With the advancement of technology, the industry shifted to preventive maintenance, which schedules regular maintenance based on average life expectancy of equipment. However, this too can be inefficient, as it leads to unnecessary maintenance and downtime.
Predictive maintenance emerges as a superior strategy by utilizing real-time data and predictive analytics to make informed decisions about when maintenance should occur, thus optimizing the maintenance schedule and extending equipment longevity.
Implementation of Predictive Maintenance
The implementation of predictive maintenance in the energy sector involves several sophisticated steps:
- Sensor Deployment: Extensive arrays of sensors are installed on critical equipment to continuously monitor various operational parameters such as vibration, temperature, and pressure.
- Data Integration and Analysis: The sensor data is integrated with historical maintenance records and operational data. Advanced AI algorithms analyze this integrated data to identify patterns and anomalies that may indicate potential failures.
- Predictive Analytics: Machine learning models process the analyzed data to predict potential points of failure. These insights allow for maintenance to be proactively scheduled at just the right time, thereby avoiding unexpected equipment failures and associated costs.
- Maintenance Optimization: AI-driven insights ensure that maintenance is performed only when necessary, which optimizes resource allocation, reduces operational costs, and minimizes equipment downtime.
Strategic Benefits
The strategic deployment of predictive maintenance offers manifold benefits to the energy sector:
- Cost Efficiency: By predicting equipment failures before they occur, companies can avoid the exorbitant costs associated with unplanned downtime and emergency repairs.
- Increased Equipment Longevity: Regular, need-based maintenance extends the life of expensive machinery and infrastructure, yielding a better return on investment.
- Enhanced Safety: Predictive maintenance significantly reduces the risk of catastrophic failures that could endanger workers and the environment, thereby supporting compliance with safety regulations and reducing liability.
- Energy Efficiency: Well-maintained equipment operates more efficiently, consumes less power, and therefore, reduces the overall environmental footprint of energy production.
As we look to the future, the role of predictive maintenance in fostering more resilient and efficient energy systems is undeniable. With continuous advancements in AI and IoT technologies, predictive maintenance is set to redefine traditional approaches to energy management, making it a pivotal element in the evolution of the global energy landscape.